What is Porosity in Welding: Finest Practices for Staying Clear Of Porous Welds
Wiki Article
Comprehending Porosity in Welding: Discovering Reasons, Results, and Avoidance Techniques
Porosity in welding is a relentless obstacle that can significantly impact the top quality and honesty of welds. As specialists in the welding market are cognizant, recognizing the reasons, impacts, and avoidance techniques associated with porosity is critical for achieving durable and trusted welds. By diving into the source of porosity, analyzing its harmful effects on weld top quality, and checking out reliable avoidance approaches, welders can boost their expertise and skills to create premium welds consistently. The complex interplay of variables contributing to porosity calls for a comprehensive understanding and an aggressive approach to make sure successful welding outcomes.Typical Reasons For Porosity
Contamination, in the form of dirt, oil, or corrosion on the welding surface, produces gas pockets when heated up, leading to porosity in the weld. Incorrect protecting happens when the protecting gas, frequently used in processes like MIG and TIG welding, is incapable to fully secure the molten weld swimming pool from responding with the surrounding air, resulting in gas entrapment and succeeding porosity. Furthermore, inadequate gas protection, usually due to incorrect flow prices or nozzle positioning, can leave parts of the weld unsafe, allowing porosity to create.Results on Weld Quality
The visibility of porosity in a weld can substantially compromise the total top quality and integrity of the welded joint. Porosity within a weld develops spaces or cavities that deteriorate the framework, making it more prone to splitting, corrosion, and mechanical failing.In addition, porosity can hinder the effectiveness of non-destructive screening (NDT) strategies, making it testing to discover various other defects or discontinuities within the weld. This can cause significant safety worries, specifically in critical applications where the architectural stability of the welded parts is paramount.
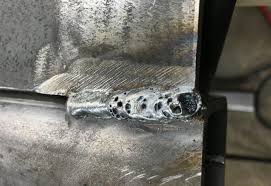
Prevention Techniques Overview
Given the destructive impact of porosity on weld quality, effective avoidance strategies are essential to maintaining the architectural integrity of welded joints. In addition, choosing the appropriate welding criteria, such as voltage, existing, and travel speed, can help minimize the threat of porosity formation. By including these prevention strategies into welding techniques, the incident of porosity can be significantly minimized, leading to stronger and a lot more trustworthy welded joints.Significance of Correct Shielding
Correct shielding in welding plays an important duty in stopping atmospheric contamination and ensuring the stability of bonded joints. Securing gases, such as argon, helium, or a blend of both, are typically used to shield the weld pool from reacting with elements in the air like oxygen and nitrogen. When these responsive aspects enter call with the hot weld pool, they can cause porosity, causing weak welds with decreased mechanical homes.
Poor protecting can result in numerous problems like porosity, spatter, and oxidation, jeopardizing the architectural honesty of the bonded joint. Sticking to proper shielding methods is necessary to create top notch welds with marginal flaws and guarantee the longevity and dependability of the welded parts.
Tracking and Control Approaches
Exactly how can welders effectively check and regulate the welding procedure to ensure optimal results and protect against defects like porosity? By continuously monitoring these variables, check out this site welders can identify discrepancies from the optimal conditions and make prompt changes to prevent porosity formation.
In addition, carrying out proper training programs for welders is vital for keeping track of and managing the welding process effectively. What is Porosity. Educating welders on the importance of keeping regular criteria, such as appropriate gas protecting and travel speed, can aid protect against porosity concerns. Routine assessments and certifications can also make certain that welders excel in surveillance and managing welding processes
Furthermore, the usage of automated welding systems can improve monitoring and control abilities. These systems look here can precisely control welding specifications, lowering the chance of human mistake and making sure consistent weld high quality. By combining innovative monitoring technologies, training programs, and automated systems, welders can properly monitor and control the welding procedure to lessen porosity problems and accomplish top notch welds.
Conclusion

Report this wiki page